Vendor Managed Inventory offers better transparency and optimized logistics for grain mills
Complex processes secured with reliable inventory data
The processes in Switzerland's largest grain mill are extremely complex – every processing step, every intermediate storage and every quantity of product delivered – is meticulously recorded at Swissmill. This is made possible by level sensors from VEGA, whose measured values provide the basis for reliable monitoring of different product streams.
The granary on the Limmat river in Zurich is considered to be the largest grain warehouse in the world. 1,000 tonnes of grain is processed every day, most of which is delivered directly to the plant by rail through the city. Most of the flour, semolina and flakes are subsequently processed in large bakeries, pasta processing plants or starch factories.
The main goals of production are smooth-running processes and energy savings. Both go hand in hand sometimes. The processes in the factory have been modified so that one less processing step than most other grain mills employ is required. All product streams are monitored. This also involves working closely with the customer.
The granary on the Limmat river in Zurich is considered to be the largest grain warehouse in the world. 1,000 tonnes of grain is processed every day, most of which is delivered directly to the plant by rail through the city. Most of the flour, semolina and flakes are subsequently processed in large bakeries, pasta processing plants or starch factories.
The main goals of production are smooth-running processes and energy savings. Both go hand in hand sometimes. The processes in the factory have been modified so that one less processing step than most other grain mills employ is required. All product streams are monitored. This also involves working closely with the customer.
With modern radar level sensors, difficult measurements in the flour silo are no problem
When it comes to level measurement, flours are anything but easy to measure. For one thing, huge amounts of dust are generated during filling and the dust cloud settles only very slowly inside the silo. For another, the approximately 120 different flours all differ somewhat in their dielectric constant. Karl Dahlke, manager of the flour silos and batch logistics at Swissmill, and his deputy Simon Rochat agree that bran is the most difficult product to measure: "It has an Epsilon value of only 1.4 in the summer." And the fact that this material is stored in a very slender, 10 m high reinforced concrete silo makes precise level measurement even more difficult.
Over the years, new level sensors from VEGA were often tested here. One difficulty was that the cable of guided microwave sensors would occasionally unravel, allowing individual product grains to get stuck in it. This generated incorrect measurement signals. In the meantime this instrument type has been replaced by VEGAPULS 69 with 80 GHz operating frequency. It measures without contact and can reliably detect the medium even through thick clouds of dust.
Over the years, new level sensors from VEGA were often tested here. One difficulty was that the cable of guided microwave sensors would occasionally unravel, allowing individual product grains to get stuck in it. This generated incorrect measurement signals. In the meantime this instrument type has been replaced by VEGAPULS 69 with 80 GHz operating frequency. It measures without contact and can reliably detect the medium even through thick clouds of dust.
Reliable level measurement in a wide variety of applications
The piping network conveys the intermediate products to the roller mills. Every process step is comprehensively monitored during operation.
Levels are measured everywhere in the plant. Many different types of measuring instruments are employed for this. For example, there are 137 VEGACAP 63 capacitive probes in the wheat receiving station. However, level sensors are also used in the production of animal feed for process control. When the product is being pelletized, the pre-depot always has to be completely filled to ensure that the density of the pellets is correct. For that reason, an especially reliable measuring signal is required in the overflow cell in the pelletizing process, since further cells may or may not be opened, depending on the filling level. If the cell overflows, the dosing units shut down. Ultimately, if the situation is not rectified, even the mills are switched off. That means that the process planners need a 100 % accurate signal, otherwise the entire production plan can run off course.
The level measuring instruments handle a special, additional task in inventory measurement. Not only do they measure the levels in Swissmill‘s own 200 grain silo cells, they monitor another 150 silos that belong to their customers. "Thanks to VEGA technology, we can look directly into the customer's silos and, if necessary, place an order for them. The companies are basically handing over responsibility for their raw materials management to us," explains Dahlke. VEGA Inventory System is a web-based software for data acquisition and visualization of level data, e.g. in storage tanks and silos. It enables optimal raw materials logistics from the supplier up to the production facility.
"We greatly appreciate the collaboration with VEGA Switzerland. In the future, we’re going to rely exclusively on radar measurement technology, and wherever possible, with the high frequency of 80 GHz. The sensors are easy to replace, even in sensitive food environments, and they measure with great reliability."
Karl Dahlke, manager of the flour silos and batch logistics at Swissmill
Karl Dahlke, manager of the flour silos and batch logistics at Swissmill
Products
Further articles
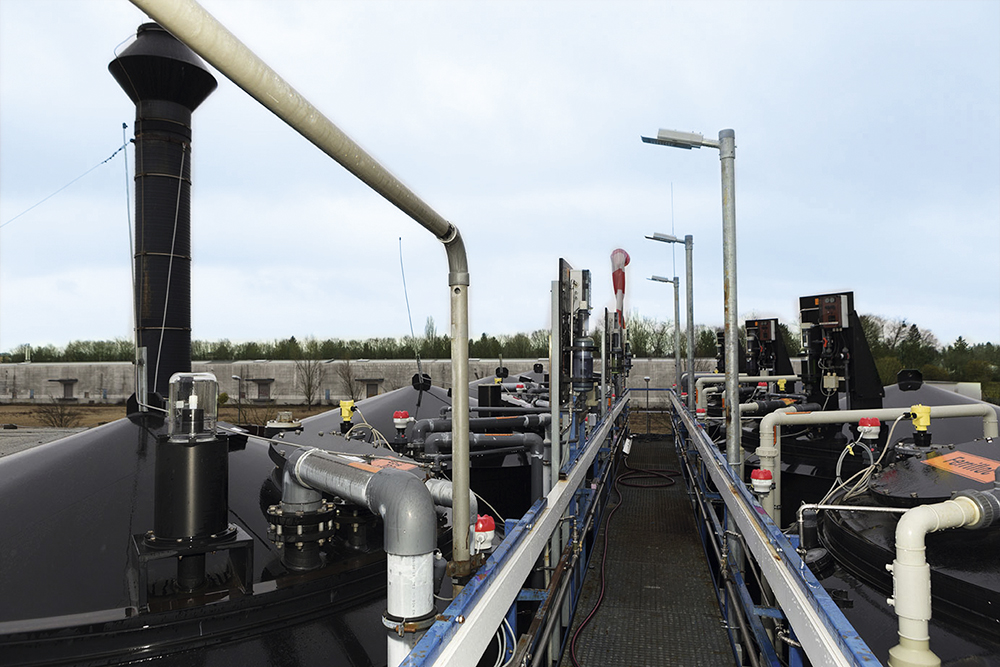
Chemicals distribution 4.0 – Digital transparency through VEGA sensors and VEGA Inventory System
Read moreExport this article
Download as PDFShare this article
Comments ({{comments.length}})
This article has no comments yet. Write the first one now!
{{getCommentAuthor(comment, "Anonymous")}} {{comment.timestamp | date : "dd.MM.yyyy HH:mm" }}
{{comment.comment}}
Write a comment
This field is mandatory
This field is mandatory
This field is mandatory
Invalid email address
This field is mandatory
Your comment must not contain any links or email addresses
This field is mandatory
Invalid captcha
untranslated: 'Blog_SendComment_Error'